
- Abaqus paraview full#
- Abaqus paraview software#
- Abaqus paraview code#
- Abaqus paraview crack#
- Abaqus paraview windows#
Abaqus paraview crack#
J-integral methods include crack face tractions, thermal loading, dynamic effects and finite strain plasticity. Integrated procedures to compute J-integrals, stress-intensity factors (KI, KII, KII) and T-stress values using domain-based and interaction integral methods. User-defined initial (residual) stress fields, including support for user-routine SIGINIįunctionally graded materials (linear-nonlinear) supported by definition of all material properties at structure nodes Simplified definition of eigenstrains to model residual stresses Mesh regularization methods for ductile crack growth simulations (several options) Node release and element extinction for crack growth (adaptive damage accumulation) User-specified multi-point constraints, periodic boundary conditions
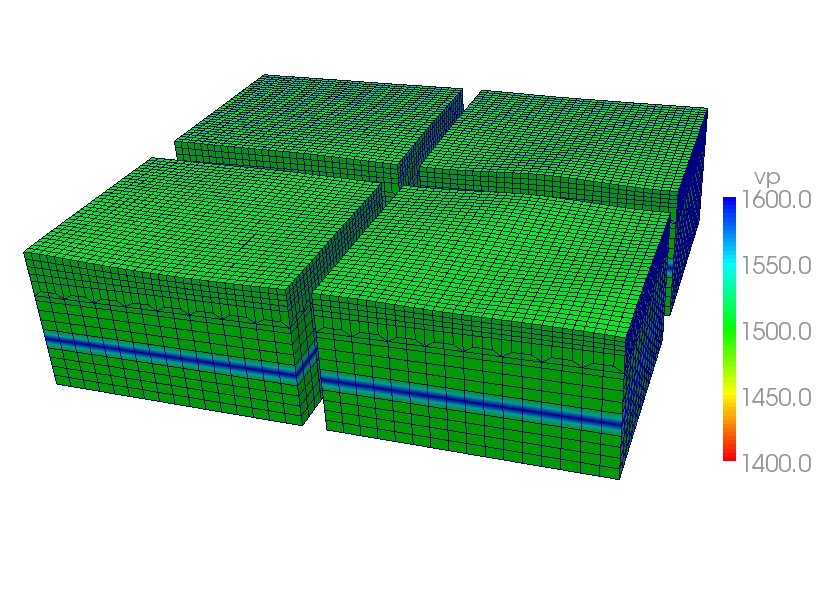
Mesh-tieing with automatic generation of multi-point constraints Non-global, absolute coordinate systems at nodesĮlement block data architectures throughout for vector/threads parallel and MPI-parallelĪrbitrary rigid body contact (frictionless) Polar decomposition based, rotation neutralized finite-strain plasticityĮlastic-predictor, radial return constitutive updatesĬonsistent tangent moduli for fast convergence of Newton iterations Line search and adaptive load step logic to assist global Newton iterations Time history integration with Newmark's beta method
Abaqus paraview full#
Incremental-iterative, implicit formulation with full Newton iterations Some Key Modeling Features and Algorithms in WARP3D Note: our research group does not have a business relationship with either MSC.Software, Quest Reliability, or Kitware.
Abaqus paraview code#
The FEACrack developers collaborate with our group to provide users with fully updated access to WARP3D capabilities and have contributed source code contained in the open-source distribution.

Abaqus paraview software#
The FEACrack software includes the latest release of the standard WARP3D distribution for Windows. FEACrack incorporates extensive, direct support for WARP3D to generate complete models containing cracks, to drive the execution of WARP3D for nonlinear analyses and to post-process results including specialized features for fracture parameters.
Abaqus paraview windows#
The company Quest Integrity Group offers the commerical software FEACrack that provides fully-integrated mesh generation and post-processing capabilities for complex fatigue and fracture analyses on Windows computers. The flat results files are generated directly in WARP3D via output commands (they are text, stream or compressed text files). The WARP3D distribution includes a Python 3 program ( warp3d2exii) that converts the flat description file for the model (written out by WARP3D) and flat files of node/element results files into an EXODUS II file (.exo) compatible with ParaView (developed by Kitware, Inc., Sandia National Laboratories, and others). Simple flat files of the model description and nodal/element results are used to interface with ParaView (these files are designed to be read very efficiently by simple Python programs, C++, C, Fortran programs and spreadsheets).
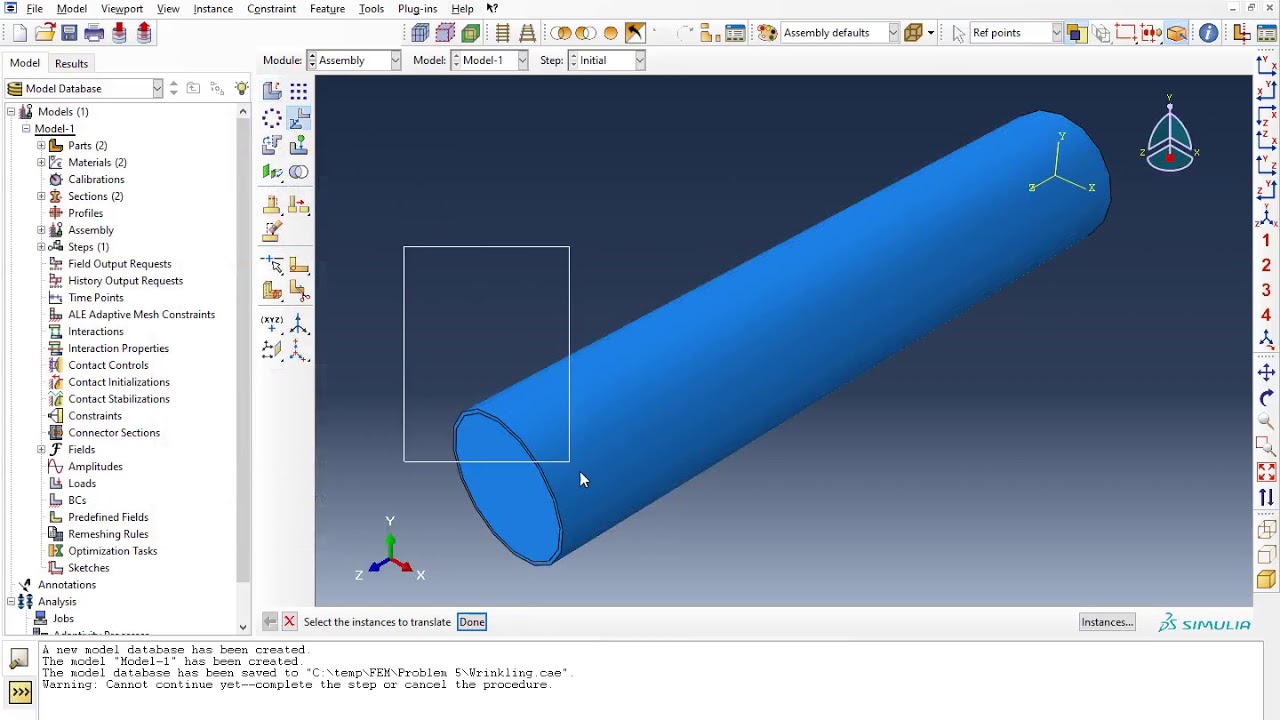
Cubit, ParaView, Patran and FEMAP, for example, are known to be used used extensively by WARP3D users for these tasks - WARP3D has built-in features to interface with Patran for model construction and post-processing through standard Patran (2.5-style) neutral files and formatted/binary files of nodal and element results. Other (graphical) programs are used to generate models and to post-process the results. WARP3D uses a text-file based input and output system. The crystal plasticity material model offers extensive features. Interfaces for Abaqus style UMAT and UEXTERNALDB routines support ready inclusion of user-defined capabilities. Some features in the code are oriented toward the investigation of fracture in metals include a robust finite strain formulation, a general J-integral computation facility (with inertia, thermal, face loading, residual stresses, initial plastic strains), interaction integrals for computation of linear-elastic fracture parameters (stress intensity factors and T-stress), very general element extinction and node release facilities to model crack growth, nonlinear material models including viscoplastic and cyclic, cohesive elements and cohesive constitutive models, hydrogen effects on plasticity, Norton creep, and the Gurson-Tvergaard dilatant plasticity model for void growth.
